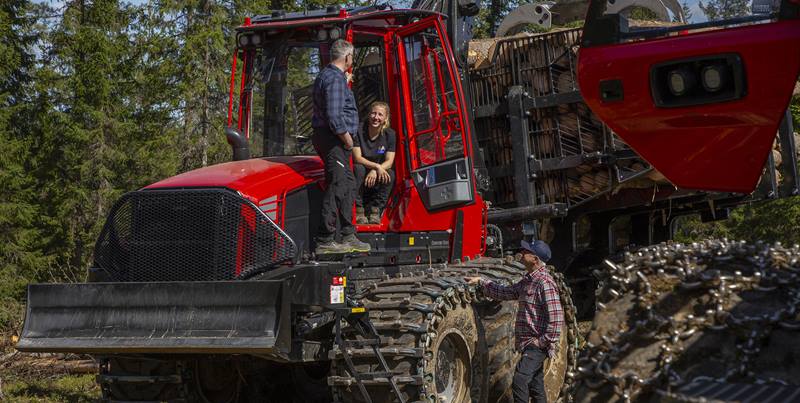
Our Customers
Creating value together
As a forest machine operator or forest machine contractor, you are one of the heroes managing our forests. You enable the processing of raw materials that become important products we all use in our daily lives.
When developing our machines, we always keep you and your working day in mind. We often invite operators and contractors to join our reference groups to provide important feedback. And when our own test operators have finished testing a new machine, it is then tested by contractors across Sweden.
This enables us to ensure that we can gather valuable insight from the people who will actually use the machines in demanding forest conditions. Below, you can partake of some of these contractors' and operators' experiences of using a Komatsu.